Miniaturization and increased capability are two of the main current trends within 3D electronics, which creates an opportunity for in-mold electronics (IME) to prove its capabilities as a new way to streamline products and create new aesthetics. IDTechEx's report, “In-Mold Electronics 2025-2035: Forecasts, Technologies, Markets“, explores the primary applications and some notable players operating within the sector. IDTechEx predicts the in-mold electronics market to reach US$974 million in 2035.
A push for IME innovation
Higher performance capabilities and reducing volume have been two of the driving forces behind IME innovations. Up until recently, the structural form factor for electronics has seen little change, with printed circuit boards (PCBs) having long been incumbent. 3D electronics can now be seen operating in a wide variety of sectors from automotive and consumer goods to sensor housing and aerospace applications.
IDTechEx explores growing opportunities to change these longstanding form factors. As a subset of 3D electronics, IME specifically involves the process of manufacturing circuitry onto a flat surface, abolishing the need for a PCB, with electrical components being mounted onto the part itself. This process typically uses screen-printing to print ink (such as conductive ink, dielectric materials, and adhesives) on a substrate such as polycarbonate, which is then molded into a 3D shape using thermoforming followed by injection molding, ultimately requiring less material than previous structural electronics methods.
IME components using far less plastic ultimately means they can be produced to be thinner and more streamlined, while generating less material costs due to there no longer being a need for as many individual components. IDTechEx reports that the existence of the in-mold decorating (IMD) market means that IME capabilities could quite feasibly be included into these companies' manufacturing processes, with little need for IME to start from scratch.
The IME value chain – from materials to machines
At the start of the IME value chain sits material suppliers, where multiple substrate options and functional and graphic inks can be selected to suit specific applications. Many conductive ink companies provide functional inks to IME manufacturers; information on which can be found in IDTechEx's report, “Conductive Inks Market 2024-2034: Technologies, Applications, Players”.
IME technology developers are positioned in the middle. With the important job of physically creating and assembling IME circuitry, IDTechEx reports that many of these developers come from a human-machine interface background, as existing manufacturing equipment can be utilized in the process. High-volume production is then carried out by manufacturers to meet the demands of end users, where the electronics can be shaped into a final product. Consumer device manufacturers, automotive OEMs, or aircraft manufacturers are positioned at the final end of the IME value chain, whereby the desired product can be designed around the streamlined circuitry.
IME applications and a growing automotive share
Smoke and carbon monoxide detectors and smart locks are some of the common applications for IME so far, though IDTechEx reports that the automotive sector is likely to see the largest increase in volume uptake of IME compared with some of these other sectors, specifically between 2027 and 2030. HMI surfaces within automotive interiors, including steering wheels, window switches, and center consoles, all create an opportunity for IME adoption, making use for drivers and passengers feel more seamless.
IME parts used for cradle-to-gate could also reportedly reduce carbon dioxide emissions from vehicles by approximately a third due to the reduction in weight and subsequent reduced fuel consumption. This will not only be beneficial for the environment but for automotive companies as they continue to reach emission reduction goals.
The reduced plastic use and subsequent environmental benefits of IME, in addition to new electronic design capabilities, result in IME becoming an estimated US$974 million market in 2035, according to IDTechEx.
For more information on IME applications and players within the market, see IDTechEx's report, “In-Mold Electronics 2025-2035: Forecasts, Technologies, Markets“. Downloadable sample pages are available for this report.
For the full portfolio of printed and flexible electronics market research available from IDTechEx, please see www.IDTechEx.com/Research/PE.
Seamless Surfaces with In-Mold Electronics
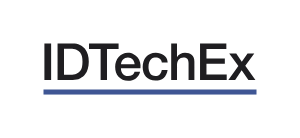