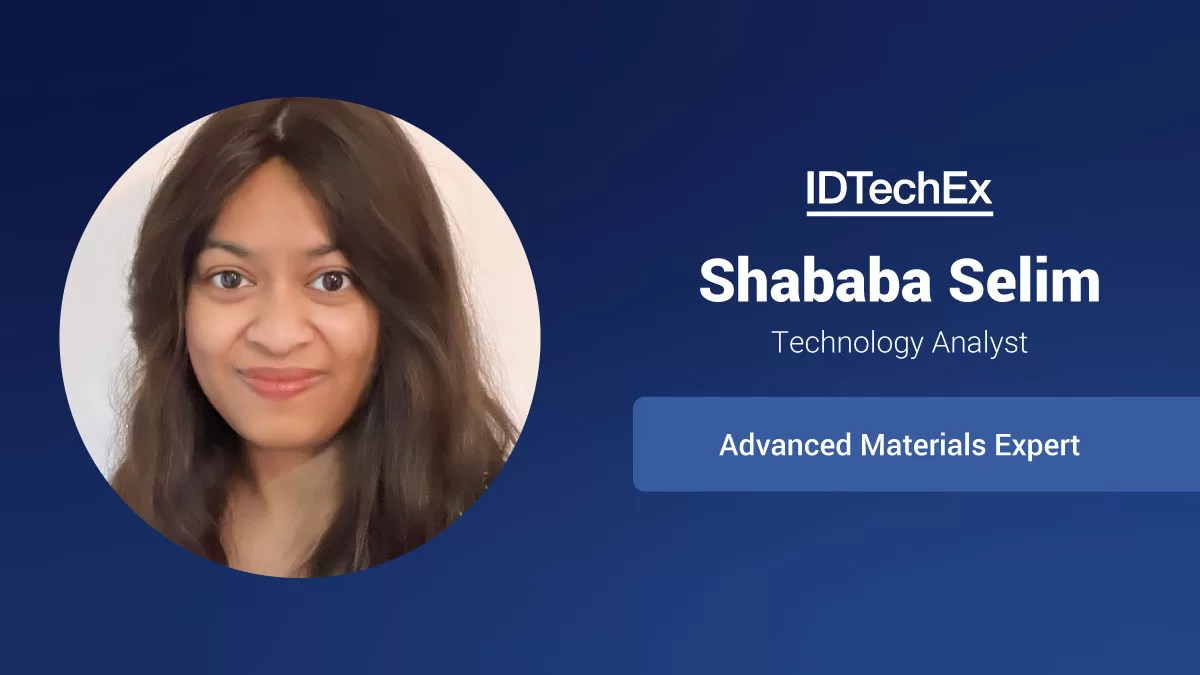
Author: Dr Shababa Selim, Technology Analyst at IDTechEx
Metal-organic frameworks (MOFs) are a class of materials with exceptionally high porosity and surface area (up to 7000m2/g). The design flexibility and structural versatility afforded by MOFs have attracted widespread interest in numerous applications, albeit with several unsuccessful attempts to commercialize the materials historically. However, these materials' tunability, cycling stability, and selective adsorption/desorption characteristics are opening opportunities for commercialization as energy-efficient alternatives for a range of critical energy-intensive technologies. These include carbon capture, water harvesting for potable water production and HVAC systems, and various chemical separations and purification processes (e.g., refrigerant reclamation and direct lithium extraction). Despite challenges, the brand new IDTechEx report, “Metal-Organic Frameworks (MOFs) 2024-2034: Market, Technology, and Players”, predicts the MOFs market to reach US$685 million by 2034.
Historically, one of the primary obstacles that has hindered the widespread commercialization of MOFs has been the prohibitive manufacturing costs, which in turn manifested in high market prices. However, recent initiatives by startups and established industry players, such as BASF, to strategically scale up the production of commercially viable MOFs can prove pivotal in reducing these costs. Together with the unique performance characteristics afforded by these materials, there is potential to position MOFs as a more competitive option to replace incumbent energy-intensive technologies, which can also encourage wider market adoption.
Recent developments in upscaling MOF production
With over 100,000 different MOF structures, only a handful meet the criteria for potential commercialization. In the last year, several developments have come to the fore in a drive to commercialize MOFs, with material manufacturers announcing steps towards industrial-scale manufacturing capabilities. Examples include US-based Numat announcing the construction of 2 industrial-scale manufacturing facilities in Chicago and Wisconsin, while BASF announced the ability to produce the MOF, CALF-20, at a scale of several hundred tonnes per year for carbon capture applications. BASF also disclosed to IDTechEx that it is working with several startups to upscale the production of a few other MOFs. Additionally, UK-based Promethean Particles told IDTechEx that it is accelerating efforts to increase its production capacity and downstream processing capability, resulting from a surge in demand into the region of metric tonnes per day by early 2026.
Using insights gained from interviews with key players, IDTechEx’s report “Metal-Organic Frameworks (MOFs) 2024-2034: Market, Technology, and Players” critically assesses the merits and challenges of the various approaches undertaken by manufacturers to upscale MOF production. Informed by primary research, the report also addresses the factors that impact the production costs and, ultimately, the selling price of MOFs.
A key utilization of MOFs: Carbon capture
Deploying carbon capture technologies is an important tool for meeting net zero emission goals. However, despite the fair level of maturity of amine solvent-based methods (i.e., amine scrubbing) to capture CO2, deployment is still limited, mainly due to the large installation cost and energy consumption associated with solvent regeneration. MOF-based modular solid sorbent carbon capture systems are gaining momentum, driven by significantly reduced energy requirements for sorbent regeneration, improved sorbent stability, CO2 selectivity, and lower capital expenditure compared to solvent-based systems.
The IDTechEx report examines the material properties and strategies to tune capture performance and assesses the progress in point source and direct air capture applications. Through interviews with players such as Nuada, AspiraDAC, and others, the market activity and outlook of systems being developed by players are addressed with comparisons of technology readiness levels and commercial opportunity.
MOFs for water harvesting and HVAC technologies
Atmospheric water harvesting (AWH) technologies using advanced sorbents (e.g., MOFs) offer an opportunity to harness water resources in regions where traditional water sources are limited. Additionally, heating and cooling effects induced by water adsorption and desorption properties of MOFs can also be used for heating, ventilation, and air conditioning (HVAC) systems that can operate with up to 70% reduced electricity consumption compared to conventional vapor compression refrigeration technologies. This can facilitate the reduction in energy consumption by HVAC systems, which currently account for ~10% of all global electricity consumption and is expected to triple by 2050 with the surge in demand, especially in the Asian market.
Additionally, a significant reduction in the production of HFC refrigerants is expected in line with the Kigali Amendment, and MOF-based systems can prove a viable alternative. IDTechEx’s report covers material and technology advances in AWH and HVAC systems that integrate MOFs and compares the key performance metrics with other sorbents. The report also highlights the key players at the forefront of developing and commercializing these technologies.
Opportunities in chemical separations and purification
Chemical separation and purification constitute core operations of manufacturing industries such as chemical production, mining, and oil and gas refining. Conventional distillation-based thermal chemical separation processes have significant drawbacks: they require a large spatial footprint, substantial capital expenditure, and are very energy-intensive. Globally, this accounts for an estimated ~10-15% of total energy consumption.
The tunable chemical selectivity and controllable pore architecture of MOFs enable selective separation of chemicals when used as solid sorbents or membranes. For example, MOF-based membrane manufacturer UniSieve told IDTechEx that it has demonstrated the separation of chemicals that have boiling points within ~5°C using its non-thermal membrane technology, which would otherwise require energy-intensive thermal separation using ~100m high distillation columns. Advances in applications such as refrigerant reclamation, direct lithium extraction, and several gas separation and purification processes such as biogas upgrading, and polymer grade propylene production, and more are evaluated within IDTechEx’s research.
IDTechEx outlook
The varied applications of MOFs present a large scope for the adoption of MOF-based technologies, particularly in applications where MOFs can result in a significant reduction in energy consumption and operational costs. These include carbon capture, chemical separations, and HVAC systems. However, these technologies have not yet been demonstrated on an industrial scale, and novel technologies can be considered risky, which may become a barrier to early adoption. Additionally, incumbent technologies have a stronghold in the key target markets, and MOFs may struggle to gain market share.
With the advent of several commercial products over the next decade, MOF-based technologies will need to demonstrate their performance at scale. This must also be complemented by a sustained growth in manufacturing capacity using scalable methods.
IDTechEx’s new report, “Metal-Organic Frameworks (MOFs) 2024-2034: Market, Technology, and Players”, offers an independent analysis of these trends and considers applications of MOFs for several other early-stage technologies, including hydrogen storage, energy storage, sensors, and more. Informed by insights gained from primary research, the report analyzes key players in the field. It provides market forecasts in terms of yearly mass demand and market value segmented by application.
|
||